Passing Down the Founder’s Skills and Spirit to the Next Generation Shaping the Future with Craftsmanship at Its Core
- Metal mining
- town planning
- Unique Products & Services
- Connecting with People
- Creative
Osaka
Founded in 1940, Akasaka Mold Engraving Studio (located in Yao City, Osaka Prefecture) is a manufacturing company specializing in injection mold production, engraving, and metal processing.
The founder, the first-generation Hyonosuke Akasaka, came from a family of doctors. He moved to Osaka from Wakayama and established the "Akasaka-style Half-Moon Engraving Method," which utilizes a traditional "half-moon single-edged blade" that craftsmen traditionally sharpen themselves when carving sculptures and Buddhist statues.
After returning to Japan following the end of World War II, Hyonosuke Akasaka I declared, "From now on, I will dedicate my work to Japan's reconstruction." With this resolve, he expanded into metal processing to contribute to Japan’s industrial and manufacturing sectors.
In the postwar era, Akasaka Mold Engraving Studio has produced not only molds for plastic products but also specialized experimental components for university and corporate research laboratories, decorative items crafted from solid silver through complete metal carving, and various steel materials, including duralumin.
Today, we speak with Hyonosuke Akasaka III, who has inherited this legacy.
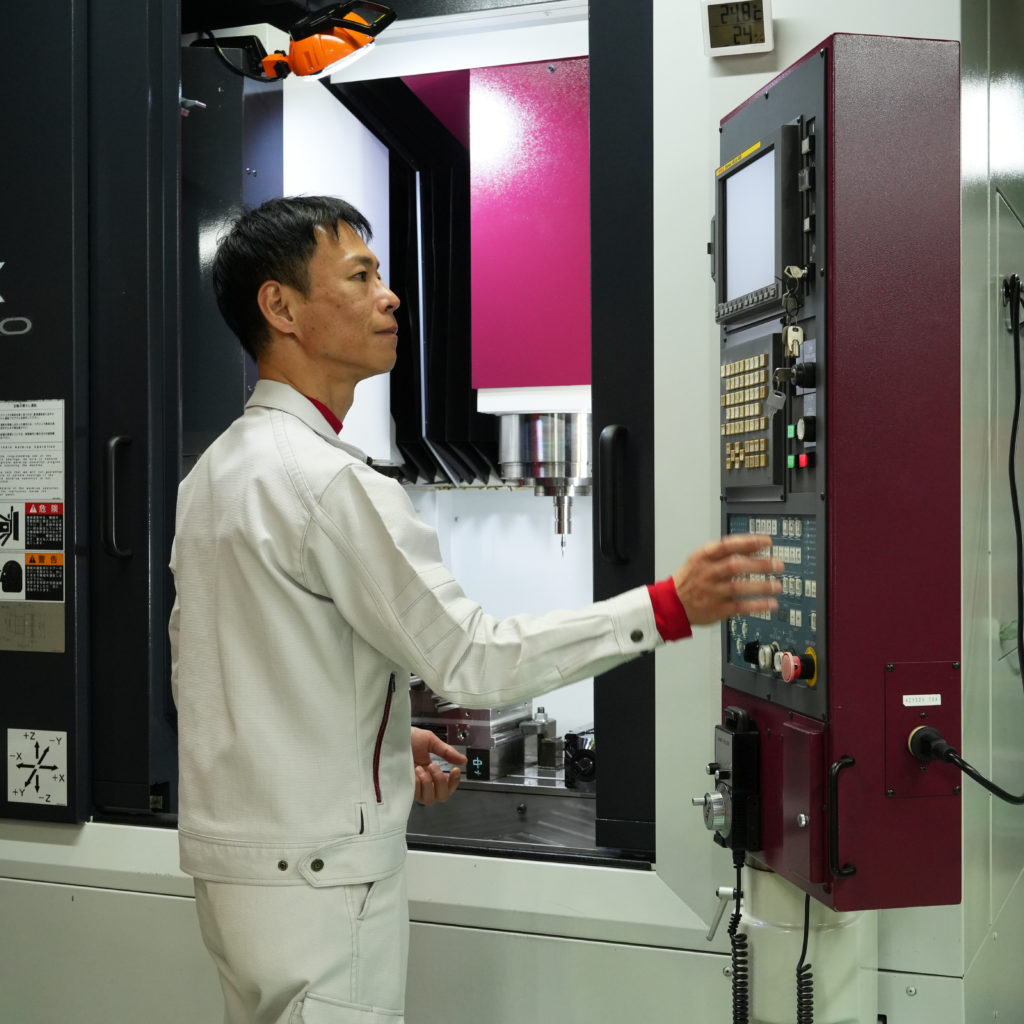
PROTAGONIST
Hyonosuke AkasakaIII
The Tradition and Craftsmanship of Akasaka Mold Engraving Studio
The company’s delicate and highly precise engraving technology has greatly contributed to Japan’s postwar industry, particularly in the production of molds essential for shaping plastic products. The indispensable tool for these intricate machining processes is the half-moon single-edged blade.
The half-moon single-edged blade is crafted by cutting a special metal rod in half and sharpening its tip to a fine point. It boasts an exceptionally sharp cutting edge and a unique property that prevents cutting debris from adhering to it. Due to its effectiveness not only on general metals but also on precious metals and resins, combining it with state-of-the-art machining technology allows for the intricate three-dimensional reproduction of complex designs and corporate logos, expanding new possibilities in the field of 3D machining.
Hyonosuke Akasaka III explains, “We create engravings, as well as molds and experimental tools. One of our achievements in engraving technology is the three-dimensional carving of the ‘Dassai’ logo on the top cap of the sparkling sake produced by Asahi Shuzo, a sake brewery in Yamaguchi Prefecture. This sake, including its sparkling variety, was given as a souvenir to foreign dignitaries by former Prime Minister Abe. Additionally, we have produced specialized curved surface stamping dies for ‘Ozeki,’ a sake brewery in Hyogo Prefecture, to engrave markings on ‘chirori,’ a vessel used to warm sake. In injection-molded products, we have engraved the delicate rose design on the container of ‘Miracle Coach Cream (Cinderella),’ a luxury cosmetic from Oppen Cosmetics, based in Osaka. All of these engravings were made using the ‘half-moon single-edged blade’ and executed with the ‘Akasaka-style Half-Moon Engraving Method,’ which has been passed down from my grandfather’s generation.”
Recently, the company has also been focusing on designing and manufacturing molds for biodegradable resin (PLA) products, as well as creating original jewelry and accessories through complete metal carving, under its unique brand, “cocur”.
Regarding the method, he explains, “The machine accurately reproduces the data created on a computer. Since it’s a machine, it excels in reproducibility, ensuring that identical pieces are consistently produced. The ‘half-moon single-edged blade’ allows for even finer engraving because its sharp tip rotates during the process. The workflow involves precise engraving by the machine up to a certain point, followed by the final finishing touches done by human hands. In the past, everything was entirely handmade by artisans. Today, machine engraving of metal is no longer uncommon. However, not only is the final finish done by hand, but the ‘half-moon single-edged blade’ itself is also hand-sharpened by artisans. This ensures that each finished piece reflects the unique individuality and philosophy of the craftsman.”
Hyonosuke Akasaka III has received numerous awards, including the “Yao Master of Craftsmanship”, the “Osaka Excellent Manufacturing Company Award”, the “Ministry of Health, Labour and Welfare’s Meister of Manufacturing”, and the “Osaka Prefecture’s Naniwa Master Artisan”. His exceptional technical skills and design sense have earned him high recognition.
The loss of my grandfather’s left hand became the turning point.
One day, Hyonosuke Akasaka I, the founder of Akasaka Mold Engraving Studio, lost his left hand in an accident involving an injection molding machine—one that had certainly been properly installed before the incident occurred.
“My father, the second-generation successor, was a schoolteacher at the time. However, after my grandfather’s accident, he decided to leave his job and take over Akasaka Mold Engraving Studio. I believe he felt it was his duty to continue the business. But on the very day my grandfather was discharged from the hospital, he crafted his own prosthetic hand using only one hand and immediately returned to his engraving work. When I first heard this story, I felt that my grandfather possessed not just the passion of a craftsman, but an unshakable determination—something far beyond mere dedication,” recalls the third-generation successor.
Later, Hyonosuke Akasaka I fully regained his ability to engrave even the finest details, despite using a prosthetic hand. He built an impressive track record and gained widespread recognition. As work continued to increase, Akasaka Mold Engraving Studio became an indispensable force in industrial development.
During the era of Hyonosuke Akasaka II, Japan entered a period of mass production and mass consumption of industrial goods.
“Today, plastic is often seen as a villain due to issues like marine plastic pollution, but back then, Japan was striving to catch up with and surpass the United States. Everyone was working hard to make molds, produce plastic through injection molding, and rapidly manufacture and consume products. That was the era when plastic products became widespread. Molds are essential for mass production—without them, manufacturing wouldn’t be possible. That’s why there was such a strong demand for molds at the time,” he explains.
Hyonosuke Akasaka III grew up immersed in the family business from a young age. By elementary school, he was already working on-site, helping with various tasks. In middle school, he operated machines controlled by computers that only he could manage. By high school, he was fully supporting the business. There were even times when his school announced over the PA system, “Please go home immediately; your family business needs you,” prompting him to rush home.
“I was always surrounded by my parents’ factory and machines. Ever since kindergarten, I would play in the workshop, making things. One of my earliest memories is polishing small copper fragments and carefully grinding them into a six-sided die. When I was in middle school, my parents once asked me what I wanted to do in the future. Without hesitation, I answered, ‘I will work in our family business.’ It wasn’t even a conscious decision—it was simply the way things were. In the Akasaka family, work and personal life were never separate; creating things was as natural as breathing. Looking back, I realize how unique that environment was. There was never any doubt or hesitation about inheriting the business, nor did I consider any alternatives. When I took over as the company’s representative from my father, it felt natural, like something I was meant to do for life. I never once thought about working for another company. Even when my university research lab invited me to stay, I turned down the offer.”
While in university, Hyonosuke Akasaka III majored in electronics and electrical engineering. He was so dedicated to his studies that he was invited to remain in academia. However, his love for the family business was even stronger. The work had become a part of him, making his succession of the company a natural and inevitable transition.
Turning Imagination into Reality
“Bringing an image or idea that exists only in someone’s mind into the real world—that, to me, is what manufacturing is all about. Things that have never existed before, things that once belonged only to the realm of imagination, suddenly take shape before our eyes, becoming tangible. The thrill, the surprise, and the joy of that moment—aren’t these the essence of craftsmanship? It feels almost like being a magician.”
The Akasaka-style Half-Moon Engraving Method is a very old technique, yet it enables the creation of delicate and highly intricate engravings. “If only I could share this craftsmanship with today’s younger generation through new and innovative means,” muses Hyonosuke Akasaka III.
Inheriting craftsmanship means developing old traditions through new methods—in other words, “fueki ryūkō” (preserving the essence while embracing innovation).
“The spirit and technical skill of the first generation represent true craftsmanship, and today, these have been distilled through the evolution of machines. Times change, and technology advances, so the trend toward automation is inevitable. However, the outcome always depends on how people use machines and tools. Just like a single blade that adapts its role depending on the situation. That’s why I am deeply grateful for the skills and experiences I have gained by learning directly from my grandfather and father—it has helped me immensely,” he reflects.
A Vision for a School Centered on Craftsmanship
The current goal of Hyonosuke Akasaka III is to establish a “School of Craftsmanship.”
*”I want to create a school centered on craftsmanship. It will be open to everyone—regardless of age, gender, or nationality, welcoming not only people from Japan but also from all over the world. Those who come to learn will not only gain technical skills but also experience Japanese culture and philosophy. We’ll share conversations over drinks and build friendships (though, to be honest, I can’t handle alcohol at all! laughs).
When these learners return to their own communities, I envision the same spirit spreading there as well. I have this image that as more and more communities around the world connect in this way, war will gradually disappear. Through craftsmanship, we can promote the philosophy of world peace, create together with like-minded people, and cultivate joy, excitement, and the thrill of making something new. That’s the kind of school I want to build.”*
Currently, Hyonosuke Akasaka III travels around the region as a craftsmanship instructor, earning his vocational training instructor certification and dedicating himself to developing young talent in companies as a “Manufacturing Meister” certified by the Ministry of Health, Labour and Welfare. His efforts go beyond passing down technical skills—he also shares ways of thinking and philosophies embedded in culture.
“In the end, no one can achieve anything alone. Times change, and technology advances, so if we don’t constantly keep fueki ryūkō (preserving the essence while embracing innovation) in mind, we risk being left behind. People can’t move forward without the help of others, and at the same time, we must also help those around us. In this era of crisis, everyone holds their own sense of justice. But precisely because of this, I believe we need to activate what I call a ‘community mechanism’—to foster like-minded individuals who can make better choices together through craftsmanship,” he explains.
At the core of his vision lies the spirit of harmony, which will undoubtedly propel him toward realizing his dream of establishing a school.
The journey of Hyonosuke Akasaka III, the third-generation president of Akasaka Mold Engraving Studio, will continue. With 84 years of history behind him, he carries forward the craftsmanship and spirit of his grandfather, the company’s founder, striving to pass them on to a new era through innovative means.
INFORMATION
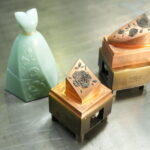
赤坂金型彫刻所
Akasaka Mold Engraving Studio is a workshop that has been engaged in mold and craft engraving, based on engraving techniques passed down through three generations.
Since the time of the first-generation artisan, Hyōnosuke Akasaka, the studio has developed its own unique engraving methods through continual innovation. It values flexible craftsmanship that adapts to the times. Today, the third-generation artisan inherits this spirit and technique, while embracing both traditional processing and new challenges.
- Founded in
- 1940
- Website
- https://www.cho-cocu.com/
- Writer:
- GOOD JOB STORY 編集部