The Beauty Depicted in Every Stitch and Thread: 126 Years of Embroidery Tradition
- Textile industry
- 100 Year Company
- Connecting with People
- Japanese Traditional Technology
Kyoto
Celebrating its 126th anniversary, Miyagawa Co., Ltd. manufactures and sells kimonos, obis, and other related products. As the fourth-generation head of the family business Miyagawa Co., Ltd. (located in Nakagyo-ku, Kyoto City), President Masahiro Miyagawa has been producing high-quality embroidery for nearly 40 years, sharing his meticulous craftsmanship with the world.
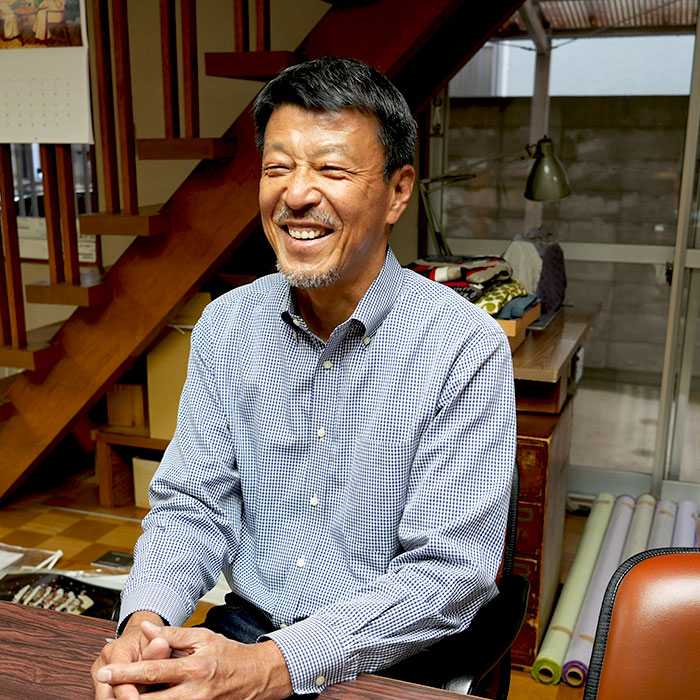
PROTAGONIST
Masahiro Miyagawapresident
Objectively Viewing the Continuation of the Company and Tradition
Miyagawa Co., Ltd. was founded by Tomekichi Miyagawa in Nakagyo-ku, Kyoto City, in the 30th year of the Meiji era. Although the company faced a temporary interruption due to the post-war corporate control order, it resumed operations five years later. In 1971, it became a corporation and was established as Miyagawa Co., Ltd.
In April 2009, the company launched its website and established the brand “Kyobebeya,” starting its online auction business in December of the same year.
Mr. Miyagawa, in discussing the secrets of maintaining and continuing the family business, states, “When considering the company first, the answer is clear. Being able to decide when to retire is rather a blessing.” He emphasizes the importance of clarifying succession to the next generation and determining the timing of retirement. While family-run businesses face complications due to social ties, he believes that separating the company from the residence and thinking objectively, without being constrained by positions, allows for a grateful succession of the family business and a diligent approach as an artisan.
In terms of production, the embroidery process involves creating embroidery color instruction data based on designs from customers and using specialized machines. While the actual embroidery is done by machines, the designs are meticulously hand-drawn over time. Colors are selected from 1,426 options, using fine threads to create depth and achieve a natural expression.
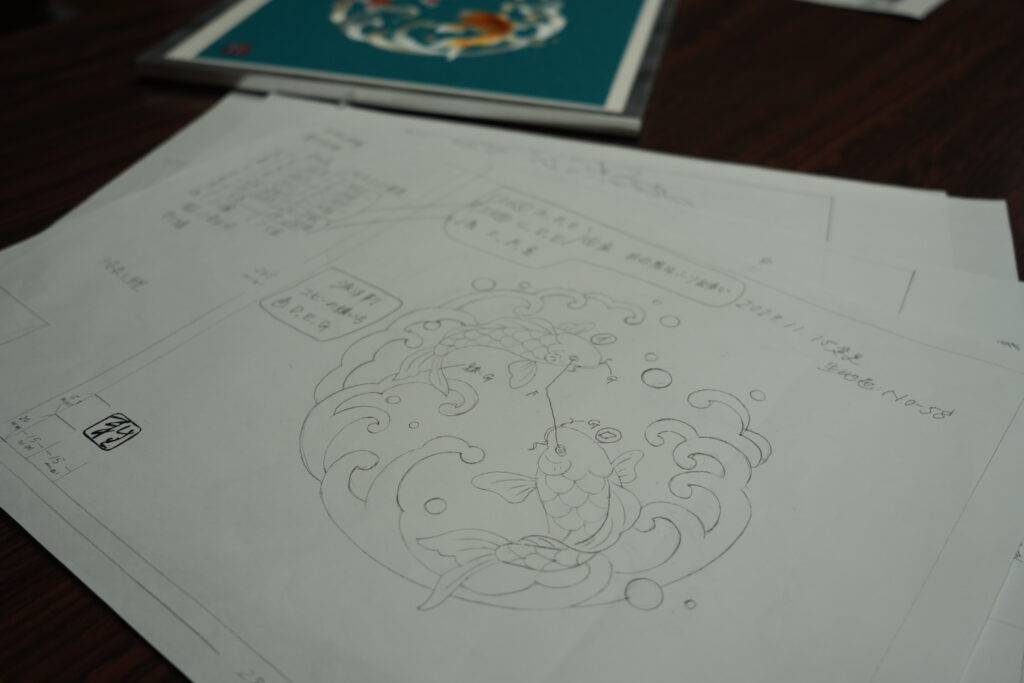
President Miyagawa comments, “It takes time, but incorporating human sensibility allows us to create something truly excellent.”
Founding Motivation
In Tango, Kyoto Prefecture, the surname “Itoi” is quite common. The founder, originally named Tomekichi Itoi, was adopted into the Miyagawa family, becoming Tomekichi Miyagawa. Tango is a region with high humidity, which reduces static electricity, making it an ideal environment for weaving and fostering the textile industry. Additionally, the availability of high-quality raw silk from sericulture farmers contributed to the region’s active textile industry.
Utilizing these favorable conditions, the first proprietor established Miyagawa Shoten in Enfukuji-cho, a wholesaler of white fabrics such as obiage and haneri. Over time, the business evolved from a local shop into a corporation. The fourth-generation President Miyagawa enthusiastically states, “I love the processes and sites of craftsmanship that have been passed down through generations. I could talk with the artisans all day long.”
Selection of Materials and Commitment to Processes
The company carefully selects appropriate thread colors and materials, considering fabric types, colors, and seasonal elements. Silk thread is primarily used, which is a natural fiber made from silkworm cocoons. These fine threads are tightly bound, offering a pleasant texture and a triangular fiber structure that reflects light, giving the fabric a beautiful sheen. While using silk thread for embroidery is common in the kimono industry, it is not the main material in other industries. Due to the limited production of silk thread in Japan, Japanese silk trading companies often import it from China and Brazil. The raw silk is then processed into threads suitable for weaving and distributed to production areas.
Regarding the dyeing process, President Miyagawa explains, “We ask artisans to dye the threads for us. The dye is mixed into a liquid, and the raw silk is immersed in it, resulting in slightly different colors each time. Although we provide a color sample book to specify ‘Please use this color,’ artisans often select and use colors from their own experience and the sample book, so we leave it to their discretion.” He further explained that both silk and rayon are used, and for consistency, the rayon threads are made thinner to match the silk threads.
In the embroidery process, he stated, “Even with a single thread color, different sewing methods can express various colors. Adding more colors increases the complexity, and using many colors doesn’t always guarantee a better product. Choosing from numerous sewing techniques to express color changes and making the most of the machinery are fascinating aspects.” The company’s products are distinguished by the sheen and gloss of the embroidery. The price of the products is determined by the number of colors used and the labor involved. Generally, the more colors used, the higher the price.
The company’s continuous efforts to improve embroidery techniques, such as expressing shades and shadows with minimal color use while leveraging artisans’ skills, have garnered strong support from their fans.
Succession of Artisan Skills
President Miyagawa is concerned about the decreasing number of people who use embroidered products in their daily lives and the decline in artisans capable of handling machinery due to aging. This has led to a reduction in product proposals.
“It would be ideal if there were young artisans to inherit these skills, but if there are none, the business ends when we retire. However, our artisans have a strong spirit of inquiry and are actively pursuing new approaches even as they age, which is very encouraging. In an era overflowing with uniform products, the unique, hand-crafted original products created through analog methods are finding success. I believe that instead of a single company bearing the responsibility for a product, better results can be achieved when artisans who understand each other’s dedication come together to support the manufacturing process,” he says.
Launch and Future Development of the “Kyobebeya” Brand
In 1972, the company established a dyeing and processing department and began to focus more on fabric production and product processing. Each step of weaving, dyeing, tie-dyeing, and embroidery is imbued with the spirit of the artisans. At Kyobebeya, they handle not only traditional Japanese designs but also modern accessories. By using thinner-than-usual threads for embroidery, they can achieve delicate detailing. They produce a wide range of products, from luxurious embroideries using silk threads to chic designs with rhinestones and cute items with polka dots. The fourth-generation president stated, “Facing what changes with the times and what remains unchanged, what do we create? What do we feel? I want to carefully discern these as an artisan.” He expressed gratitude for overcoming the company’s potential bankruptcy, acknowledging the lack of competition and the fortunate relationships with customers and suppliers. Regarding the preservation of Japanese culture, he mentioned, “It would be good if artisans could go to schools to teach.” Concerning kimonos, he noted that the current demand is divided between purchase and rental, adding, “I would be happy if customers continue to enjoy using traditional crafts.” Despite concerns about the decreasing demand for embroidered products such as kimonos and obis, which require special processes, he is determined to ensure their continuation.
INFORMATION
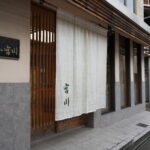
Miyagawa Co., Ltd.
We create products related to kimonos, such as kimonos themselves, obi, obiage, haneri, and obijime. In addition to producing items under our original brand "Kyobebeya," we also accept custom orders for original products from our customers. All products are exclusively original creations by Miyagawa, with no sourced products. We propose our products with the skills and refined sensibilities cultivated in Kyoto, a city known for its craftsmanship.
- Founded in
- 1897
- No. of employees
- -
- Website
- https://kyobebeya.com/
- Writer:
- GOOD JOB STORY 編集部